Featured Contents
Sample Post 1
Lorem Ipsum is simply dummy text of the printing and typesetting industry. Lorem Ipsum has been the industry's standard dummy text ever since the 1500s, when an unknown printer took a galley of type and scrambled it to make a type specimen book. [...]
Sample Post 2
Lorem Ipsum is simply dummy text of the printing and typesetting industry. Lorem Ipsum has been the industry's standard dummy text ever since the 1500s, when an unknown printer took a galley of type and scrambled it to make a type specimen book. [...]
Latest Posts
0
Vídeo demonstrando o funcionamento do Soldador Virtual
willianend
quarta-feira, 21 de julho de 2010
0
Simulador avalia processos de soldagem em ambiente virtual
willianend
Com o objetivo de avaliar soldagens e profissionais soldadores, um grupo de engenheiros, formados pela Escola Politécnica (Poli) da USP, desenvolveu um simulador de soldagens que prepara estudantes e novos funcionários em treinamento em processos seletivos. O aparelho reduz os custos para a empresa e proporciona total segurança durante o processo de avaliação.
O simulador foi desenvolvido pelos engenheiros Freddy Poetscher, Cristiano Fernandes Lagatta e João Lucas Alves, todos formados pela Poli, respectivamente em Engenharia Metalúrgica, Mecatrônica e de Materiais. Os três são sócios na Testmat Consultoria e Treinamento, uma empresa prestadora de serviços de engenharia, automação e treinamento.
Atualmente inserida no Centro de Inovação, Empreendedorismo e Tecnologia (Cietec), incubadora de empresas conveniada à USP, a empresa desenvolve projetos de ambientes virtuais para seleção de materiais. Além do Solvi, ela está desenvolvendo o Microscópio Virtual e o Pintor Virtual.
O aparelho, denominado Soldador Virtual (Solvi) é um conjunto de hardware e software que simula o processo de soldagem. Uma tocha de solda com um sensor acoplado capta os movimentos do soldador e simula, em um monitor, o cordão de solda. A avaliação da qualidade da solda leva em conta elementos como precisão, velocidade, distância, entre outros.
Poetscher explica que “o Solvi é como um simulador de avião, que tem objetivo de treinar profissionais e avaliar a perícia e o desempenho durante o processo de soldagem”. Ele será utilizado por escolas técnicas, empresas de qualidade de soldagem, em processos de seleção de soldadores.
Inovação
Poetscher ressalta que o Solvi é o primeiro simulador virtual da América do Sul, sendo que toda a tecnologia foi desenvolvida no Cietec. “Ao contrário dos concorrentes estrangeiros, que utilizam máscaras de simulação virtual, nosso simulador tem como diferencial três pontos principais: o uso de uma tocha de solda real; a possibilidade de avaliação imediata do soldador; e avaliação qualidade da soldagem, por meio de resultados objetivos sobre o desempenho do processo”, explica o engenheiro.
Segundo o Poetscher, o Solvi começará a ser comercializado ainda neste primeiro semestre de 2010, com uma parceria com o Infosolda, um portal brasileiro de soldagens. A pedidos de alguns usuários, os sócios da Testmat estudam a ideia de desenvolver a máscara para criar ambientes de realidade virtual para o simulador.
O simulador foi desenvolvido pelos engenheiros Freddy Poetscher, Cristiano Fernandes Lagatta e João Lucas Alves, todos formados pela Poli, respectivamente em Engenharia Metalúrgica, Mecatrônica e de Materiais. Os três são sócios na Testmat Consultoria e Treinamento, uma empresa prestadora de serviços de engenharia, automação e treinamento.
Atualmente inserida no Centro de Inovação, Empreendedorismo e Tecnologia (Cietec), incubadora de empresas conveniada à USP, a empresa desenvolve projetos de ambientes virtuais para seleção de materiais. Além do Solvi, ela está desenvolvendo o Microscópio Virtual e o Pintor Virtual.
O aparelho, denominado Soldador Virtual (Solvi) é um conjunto de hardware e software que simula o processo de soldagem. Uma tocha de solda com um sensor acoplado capta os movimentos do soldador e simula, em um monitor, o cordão de solda. A avaliação da qualidade da solda leva em conta elementos como precisão, velocidade, distância, entre outros.
Poetscher explica que “o Solvi é como um simulador de avião, que tem objetivo de treinar profissionais e avaliar a perícia e o desempenho durante o processo de soldagem”. Ele será utilizado por escolas técnicas, empresas de qualidade de soldagem, em processos de seleção de soldadores.
Inovação
Poetscher ressalta que o Solvi é o primeiro simulador virtual da América do Sul, sendo que toda a tecnologia foi desenvolvida no Cietec. “Ao contrário dos concorrentes estrangeiros, que utilizam máscaras de simulação virtual, nosso simulador tem como diferencial três pontos principais: o uso de uma tocha de solda real; a possibilidade de avaliação imediata do soldador; e avaliação qualidade da soldagem, por meio de resultados objetivos sobre o desempenho do processo”, explica o engenheiro.
Segundo o Poetscher, o Solvi começará a ser comercializado ainda neste primeiro semestre de 2010, com uma parceria com o Infosolda, um portal brasileiro de soldagens. A pedidos de alguns usuários, os sócios da Testmat estudam a ideia de desenvolver a máscara para criar ambientes de realidade virtual para o simulador.
0
Soldagem a eletrodo tubular pode ser automatizada
willianend
O processo une a automação da soldagem MIG/MAG juntamente com a vantagem de soldar sob escória protetora dos eletrodos convencionais. Resumidamente, é como se fosse o processo MIG/MAG, mas com escória e sem a manipulação de fluxos como no arco submerso.
Com o início da sua utilização, por volta da década de 1960, o eletrodo - ou arame - tubular aumentou a qualidade do metal de solda depositado. O processo ainda oferece excelente aparência ao cordão de solda, boas características de arco, redução do número de respingos e possibilidade de solda em todas as posições. Entretanto, ganhou popularidade para soldagem de aços carbono e baixa liga, em chapas de espessura grossa e fina.
Devido à sua versatilidade e possibilidade de aplicação em ambientes considerados hostis, a utilização de arame tubular autoprotegido ganha destaque. Ambientes subaquáticos, plataformas de prospecção de petróleo, estaleiros navais e diversos locais de difícil acesso e condições de trabalhos desfavoráveis são exemplos de seu uso.
O processo é definido como sendo uma soldagem por fusão, onde o calor necessário à ligação das partes é fornecido por um arco elétrico estabelecido entre a peça e um arame alimentado continuamente.
Com duas variantes, pode ser protegido por gás inerte, gás ativo ou a mistura de ambos (chamado de dualshield) ou autoprotegido, sem a utilização de gases de proteção (chamado de innershield). Os equipamentos utilizados nos dois processos são similares. A diferença básica é o sistema de envio e controle dos gases ao ponto de trabalho, no caso da soldagem com proteção gasosa.
Com o início da sua utilização, por volta da década de 1960, o eletrodo - ou arame - tubular aumentou a qualidade do metal de solda depositado. O processo ainda oferece excelente aparência ao cordão de solda, boas características de arco, redução do número de respingos e possibilidade de solda em todas as posições. Entretanto, ganhou popularidade para soldagem de aços carbono e baixa liga, em chapas de espessura grossa e fina.

O processo é definido como sendo uma soldagem por fusão, onde o calor necessário à ligação das partes é fornecido por um arco elétrico estabelecido entre a peça e um arame alimentado continuamente.
Com duas variantes, pode ser protegido por gás inerte, gás ativo ou a mistura de ambos (chamado de dualshield) ou autoprotegido, sem a utilização de gases de proteção (chamado de innershield). Os equipamentos utilizados nos dois processos são similares. A diferença básica é o sistema de envio e controle dos gases ao ponto de trabalho, no caso da soldagem com proteção gasosa.
0
Novo método permite soldagem entre metal e cerâmica
willianend
sábado, 17 de julho de 2010
ientistas da Universidade Johns Hopkins desenvolveram um novo método de efetuar um tipo especial de soldagem, chamado brasagem, que poderá revolucionar principalmente a área de junção entre materiais cerâmicos e metálicos. O método já está totalmente desenvolvido e disponível para a indústria. Os pesquisadores estão oferecendo a tecnologia através de uma empresa fundada por eles mesmos, a Reactive NanoTechnologies.
Os pesquisadores desenvolveram uma folha metálica reativa, de várias camadas. Quando a folha é posta em ignição, ela gera calor suficiente para juntar as duas partes, sem danificar os componentes sendo soldados.
O uso de uma única folha como fonte de calor simplifica o processo de brasagem, tornando-o mais barato. O método também evita danos para componentes sensíveis ao calor, como componentes eletrônicos e polímeros.
As folhas reativas são uma nova classe de materiais nanoestruturados que são fabricados por um método de deposição de vapor. Centenas de camadas com poucos átomos de espessura são intercaladas entre elementos como alumínio e níquel. Quando exposta a uma fonte de calor, tal como uma faísca, estes metais se misturam em escala atômica, causando uma liberação de calor que pode chegar a 1.500º C em menos de 10 milisegundos. A velocidade, temperatura e curva de aquecimento podem ser controladas variando-se a composição das folhas e a espessura das camadas individuais.
Atualmente, cerâmicas são unidas a outros componentes com a utilização de adesivos ou fixadores de vários tipos. É o caso da fixação de dissipadores de calor em chips de computador, que se utiliza de uma pasta condutora. Embora a junção metálica produza melhores resultados, permitindo maior dissipação do calor gerado, componentes metálicos e cerâmicos se contraem a taxas diferentes quando aquecidos. O aquecimento necessário para a brasagem acaba por gerar um stress nos componentes, podendo causar delaminação ou mesmo inutilizar o componente, o que limita a utilização da solda a áreas não superiores a 1 polegada quadrada.
O novo método é um grande avanço em todas as técnicas de soldagem, uma vez que toda a energia necessária para efetuar a solda origina-se da própria folha, eliminando a necessidade de elementos como gases, bicos de solda ou laser. Componentes sensíveis à temperatura, tal como componentes eletrônicos ou polímeros, não são danificados, uma vez que o aquecimento localiza-se unicamente na interface sendo soldada. Aplicações até agora impraticáveis devido a barreiras técnicas, como a junção de materiais de naturezas diferentes, como cerâmica e metal, tornam-se possíveis como o novo método.
Os pesquisadores desenvolveram uma folha metálica reativa, de várias camadas. Quando a folha é posta em ignição, ela gera calor suficiente para juntar as duas partes, sem danificar os componentes sendo soldados.
O uso de uma única folha como fonte de calor simplifica o processo de brasagem, tornando-o mais barato. O método também evita danos para componentes sensíveis ao calor, como componentes eletrônicos e polímeros.
As folhas reativas são uma nova classe de materiais nanoestruturados que são fabricados por um método de deposição de vapor. Centenas de camadas com poucos átomos de espessura são intercaladas entre elementos como alumínio e níquel. Quando exposta a uma fonte de calor, tal como uma faísca, estes metais se misturam em escala atômica, causando uma liberação de calor que pode chegar a 1.500º C em menos de 10 milisegundos. A velocidade, temperatura e curva de aquecimento podem ser controladas variando-se a composição das folhas e a espessura das camadas individuais.
Atualmente, cerâmicas são unidas a outros componentes com a utilização de adesivos ou fixadores de vários tipos. É o caso da fixação de dissipadores de calor em chips de computador, que se utiliza de uma pasta condutora. Embora a junção metálica produza melhores resultados, permitindo maior dissipação do calor gerado, componentes metálicos e cerâmicos se contraem a taxas diferentes quando aquecidos. O aquecimento necessário para a brasagem acaba por gerar um stress nos componentes, podendo causar delaminação ou mesmo inutilizar o componente, o que limita a utilização da solda a áreas não superiores a 1 polegada quadrada.
O novo método é um grande avanço em todas as técnicas de soldagem, uma vez que toda a energia necessária para efetuar a solda origina-se da própria folha, eliminando a necessidade de elementos como gases, bicos de solda ou laser. Componentes sensíveis à temperatura, tal como componentes eletrônicos ou polímeros, não são danificados, uma vez que o aquecimento localiza-se unicamente na interface sendo soldada. Aplicações até agora impraticáveis devido a barreiras técnicas, como a junção de materiais de naturezas diferentes, como cerâmica e metal, tornam-se possíveis como o novo método.
0
Pesquisadores brasileiros desenvolvem soldagem subaquática
willianend
Uma nova tecnologia que promete revolucionar os trabalhos de soldagem subaquática em alto-mar e em rios, diminuindo custos e aumentando a qualidade do processo, está sendo desenvolvida na Escola de Engenharia da UFMG (Universidade Federal de Minas Gerais). O sistema compreende um dispositivo que auxilia a abertura do arco elétrico - fonte de calor que permite a fusão dos metais no processo de soldagem - e por uma guia sextavada, peça que integra o mecanismo que controla os movimentos do eletrodo responsável pela produção do cordão de solda.
"Atualmente, a soldagem é feita pelo soldador num ambiente desfavorável, marcado pela baixa visibilidade e controle quase inexistente do equipamento", diz o professor Alexandre Bracarense, coordenador do Laboratório de Robótica, Soldagem e Simulação, do departamento de Engenharia Mecânica da UFMG, onde o processo vem sendo desenvolvido desde 1999.
O projeto é fruto de convênio entre a UFMG e a Colorado School of Mines, dos Estados Unidos, com apoio do Instituto Mexicano de Petróleo, do CNPq e do Minerals Management Service, similar norte-americano do Ministério de Minas e Energia. As primeiras pesquisas foram desenvolvidas para a aplicação de soldagem subaquática em rios.
O processo desenvolvido pelos pesquisadores mineiros está sendo testado em um tanque de cerca de 800 litros com água e ar-comprimido. O ar comprimido, forçado sobre a parte superior do tanque, pressiona a água, simulando a profundidade do mar. Dez metros de profundidade correspondem à pressão de uma atmosfera (atm) no tanque. "Cinco atms no tanque simulam a pressão de 50 metros de profundidade", exemplifica o mestrando Ezequiel Caires, da equipe do professor Bracarense.
"Atualmente, a soldagem é feita pelo soldador num ambiente desfavorável, marcado pela baixa visibilidade e controle quase inexistente do equipamento", diz o professor Alexandre Bracarense, coordenador do Laboratório de Robótica, Soldagem e Simulação, do departamento de Engenharia Mecânica da UFMG, onde o processo vem sendo desenvolvido desde 1999.
O projeto é fruto de convênio entre a UFMG e a Colorado School of Mines, dos Estados Unidos, com apoio do Instituto Mexicano de Petróleo, do CNPq e do Minerals Management Service, similar norte-americano do Ministério de Minas e Energia. As primeiras pesquisas foram desenvolvidas para a aplicação de soldagem subaquática em rios.
O processo desenvolvido pelos pesquisadores mineiros está sendo testado em um tanque de cerca de 800 litros com água e ar-comprimido. O ar comprimido, forçado sobre a parte superior do tanque, pressiona a água, simulando a profundidade do mar. Dez metros de profundidade correspondem à pressão de uma atmosfera (atm) no tanque. "Cinco atms no tanque simulam a pressão de 50 metros de profundidade", exemplifica o mestrando Ezequiel Caires, da equipe do professor Bracarense.
0
Soldagem na era espacial
willianend
Mesmo nas avançadas espaçonaves do futuro, mais cedo ou mais tarde as coisas tenderão a se quebrar. Viajantes do espaço em uma longa jornada rumo a Marte, por exemplo, necessitarão estar prontos para fazer pequenos reparos quando necessário, unindo isto, soldando aquilo.
No implacável ambiente espacial, uma solda bem feita em, por exemplo, um equipamento de navegação ou uma bomba de oxigênio, pode fazer a diferença entre a vida e a morte.
Astronauta James Voss usa um ferro de solda a bordo da Estação Espacial Internacional
"Supreendementemente, sabe-se relativamente pouco sobre a física da brasagem em microgravidade," explica Richard Grugel, um cientista da NASA especializado em solidificação de metais.
Para aprender mais sobre esse processo, Grugel e seus colegas Fay Hua, da Intel, e A.V. Anilkumar, da Universidade Vanderbilt, planejaram uma experiência a ser feita na Estação Espacial Internacional, chamada Investigação da Brasagem no Espaço (ISSI: "In Space Soldering Investigation"). Eles esperam que o experimento lance uma nova luz sobre a física da brasagem e, nesse processo, torne o ferro de solda uma ferramenta mais segura para os astronautas.
A solda fundida se comporta de forma diferente no espaço. No ambiente de microgravidade da nave, a solda fundida não "sente" um puxão prá baixo como acontece na Terra, fazendo com que a tensão superficial se torne mais marcante e faça com que cada bolha de solda líquida flutue de forma diferenciada. Em outras palavras, as técnicas de soldagem do tipo brasagem que funcionam em terra poderão não resultar nas conexões esperadas quando em órbita.
Microfotografia de solda solidificada em um fio, feita por microscópio de tunelamento eletrônico. O ângulo preciso no qual a solda se junta ao fio é dado por forças como a tensão superficial, a gravidade e a umidade do fio. Removendo os efeitos da gravidade permitirá que os físicos entendam melhor essas e outras influências.
Pior ainda, essas juntas soldadas em órbita poderão ser muito mais frágeis. Na Terra, bolhas de gás na solda fundida freqüentemente sobem à superfície e desaparecem, mas podem se manter em suspensão no interior do líquido quando em órbita. Isto se dá porque a força da gravidade é a força por detrás da flutuabilidade, de forma que as bolhas em ambiente de microgravidade não necessariamente subirão. Essas diminutas bolhas ficam presas na solda quando ela se solidifica, tornando a junção menos efetiva e mais sujeita a quebras - algo não muito bom quando você está no ambiente de missão crítica do espaço.
"Quão predominantes são essas bolhas de gás no espaço? Nós precisamos descobrir, e talvez encontrar alguma forma de retirar essas bolhas de gás de forma que possamos fazer boas junções que não se quebrem," afirma Grugel.
A experiência é simples e direta: fios de metal serão soldados em várias disposições, refletindo geometrias comuns na execução de reparos. Membros da tripulação da Estação Espacial utilizarão um ferro de solda para juntar esses fios com solda de chumbo-estanho.
Enquanto a frota de ônibus espaciais não estiver voando, o espaço para o envio de equipamentos de pesquisas e materiais para a Estação Espacial está severamente limitado. A experiência ISSI foi selecionada em parte porque ela não requer envio de peso para a Estação. A Estação Espacial já possui um kit de brasagem a bordo e bobinas de fio de cobre recoberto com prata.
A experiência será feita com fio (quadro de cima) e um kit de solda (quadro de baixo) a bordo da Estação Espacial.
A tripulação Expedição 7, que recentemente retornou à Terra, construiu os fios em formatos de L, bobinas, paralelos e outros desenhos em preparação para o experimento. Os pesquisadores esperam que a atual tripulação (Expedição 8) faça o experimento durante sua estadia, que está agendada para durar até Abril de 2.004.
Enquanto o experimento estiver acontecendo, os pesquisadores poderão acompanhá-lo ao vivo no Centro de Telesciência do Centro de Vôos Espaciais Marshall em Huntsville, Alabama. Eles estarão acompanhando para ver as diferenças no fluxo da solda e o formato que ele assume no espaço, o que poderá dar dicas sobre a física fundamental da solda fundida.
Se eles virem algo inesperado, a interação ao vivo irá permitir que sugiram alterações nos procedimentos aos membros da tripulação da Estação em tempo real. Depois que as amostras retornarem à Terra, os cientistas irão cortar as junções para ver quantas bolhas de gás foram aprisionadas durante o processo, além de testarem a resistência das junções.
"Nós deveremos ser capazes de vislumbrar como a tensão superficial afeta a brasagem em microgravidade," afirma Grugel. "Isto irá ajudar a lançar os fundamentos para o futuro da fabricação e manutenção no espaço."
No implacável ambiente espacial, uma solda bem feita em, por exemplo, um equipamento de navegação ou uma bomba de oxigênio, pode fazer a diferença entre a vida e a morte.
Astronauta James Voss usa um ferro de solda a bordo da Estação Espacial Internacional
"Supreendementemente, sabe-se relativamente pouco sobre a física da brasagem em microgravidade," explica Richard Grugel, um cientista da NASA especializado em solidificação de metais.
Para aprender mais sobre esse processo, Grugel e seus colegas Fay Hua, da Intel, e A.V. Anilkumar, da Universidade Vanderbilt, planejaram uma experiência a ser feita na Estação Espacial Internacional, chamada Investigação da Brasagem no Espaço (ISSI: "In Space Soldering Investigation"). Eles esperam que o experimento lance uma nova luz sobre a física da brasagem e, nesse processo, torne o ferro de solda uma ferramenta mais segura para os astronautas.
A solda fundida se comporta de forma diferente no espaço. No ambiente de microgravidade da nave, a solda fundida não "sente" um puxão prá baixo como acontece na Terra, fazendo com que a tensão superficial se torne mais marcante e faça com que cada bolha de solda líquida flutue de forma diferenciada. Em outras palavras, as técnicas de soldagem do tipo brasagem que funcionam em terra poderão não resultar nas conexões esperadas quando em órbita.
Microfotografia de solda solidificada em um fio, feita por microscópio de tunelamento eletrônico. O ângulo preciso no qual a solda se junta ao fio é dado por forças como a tensão superficial, a gravidade e a umidade do fio. Removendo os efeitos da gravidade permitirá que os físicos entendam melhor essas e outras influências.
Pior ainda, essas juntas soldadas em órbita poderão ser muito mais frágeis. Na Terra, bolhas de gás na solda fundida freqüentemente sobem à superfície e desaparecem, mas podem se manter em suspensão no interior do líquido quando em órbita. Isto se dá porque a força da gravidade é a força por detrás da flutuabilidade, de forma que as bolhas em ambiente de microgravidade não necessariamente subirão. Essas diminutas bolhas ficam presas na solda quando ela se solidifica, tornando a junção menos efetiva e mais sujeita a quebras - algo não muito bom quando você está no ambiente de missão crítica do espaço.
"Quão predominantes são essas bolhas de gás no espaço? Nós precisamos descobrir, e talvez encontrar alguma forma de retirar essas bolhas de gás de forma que possamos fazer boas junções que não se quebrem," afirma Grugel.
A experiência é simples e direta: fios de metal serão soldados em várias disposições, refletindo geometrias comuns na execução de reparos. Membros da tripulação da Estação Espacial utilizarão um ferro de solda para juntar esses fios com solda de chumbo-estanho.
Enquanto a frota de ônibus espaciais não estiver voando, o espaço para o envio de equipamentos de pesquisas e materiais para a Estação Espacial está severamente limitado. A experiência ISSI foi selecionada em parte porque ela não requer envio de peso para a Estação. A Estação Espacial já possui um kit de brasagem a bordo e bobinas de fio de cobre recoberto com prata.
A experiência será feita com fio (quadro de cima) e um kit de solda (quadro de baixo) a bordo da Estação Espacial.
A tripulação Expedição 7, que recentemente retornou à Terra, construiu os fios em formatos de L, bobinas, paralelos e outros desenhos em preparação para o experimento. Os pesquisadores esperam que a atual tripulação (Expedição 8) faça o experimento durante sua estadia, que está agendada para durar até Abril de 2.004.
Enquanto o experimento estiver acontecendo, os pesquisadores poderão acompanhá-lo ao vivo no Centro de Telesciência do Centro de Vôos Espaciais Marshall em Huntsville, Alabama. Eles estarão acompanhando para ver as diferenças no fluxo da solda e o formato que ele assume no espaço, o que poderá dar dicas sobre a física fundamental da solda fundida.
Se eles virem algo inesperado, a interação ao vivo irá permitir que sugiram alterações nos procedimentos aos membros da tripulação da Estação em tempo real. Depois que as amostras retornarem à Terra, os cientistas irão cortar as junções para ver quantas bolhas de gás foram aprisionadas durante o processo, além de testarem a resistência das junções.
"Nós deveremos ser capazes de vislumbrar como a tensão superficial afeta a brasagem em microgravidade," afirma Grugel. "Isto irá ajudar a lançar os fundamentos para o futuro da fabricação e manutenção no espaço."
0
Brasil vai dominar soldagem de ligas metálicas especiais em dois anos
willianend
O Laboratório Nacional de Luz Síncrotron (LNLS), em Campinas (SP), está desenvolvendo uma tecnologia para soldagem de vários tipos de ligas metálicas especiais, um processo que poderá ser utilizado pela indústria petrolífera, aeronáutica, espacial, em saneamento básico e no tratamento de água industrial, entre outras.
Telas Premium
A nova técnica de soldagem vai possibilitar a fabricação de elementos filtrantes para "Telas Premium", utilizadas especialmente para controle de areia em poços de petróleo e gás. Esse mesmo processo pode ser usado no tratamento de água industrial, filtração em alta pressão e em alta vazão, em saneamento básico, além das indústrias aeronáutica, espacial e em equipamentos científicos.
O Brasil gasta anualmente cerca de US$ 40 milhões em importação de telas desse tipo. Além da economia, o país poderá passar a disputar o mercado internacional do produto, estimado em US$ 200 milhões. Hoje, apenas três empresas no mundo dominam a tecnologia.
A grande participação brasileira nesse mercado se justifica por que a maior parte do nosso petróleo vem de poços de grande profunidade, onde a utilização das telas premium é essencial.
Domínio do ciclo completo
O ciclo completo de produção das telas premium deverá ser dominado pelo Brasil em dois anos, segundo avaliação do engenheiro Samuel Tocalino, da empresa DFB, parceira do LNLS no projeto.
O LNLS trabalha no desenvolvimento de processos especiais de soldagem há mais de 10 anos, para utilização na fabricação de componentes para os aceleradores de elétrons, linhas de luz e outros componentes do Laboratório.
Soldagens não convencionais
"A parceria para o desenvolvimento desse projeto surgiu há dois anos com o interesse comum no desenvolvimento de técnicas de soldagem não convencionais que pudessem unir diferentes materiais metálicos que podem ser utilizados tanto para a fabricação de peças para os aceleradores, como para as outras aplicações," conta o professor Osmar Roberto Bagnato, do LNLS
Telas Premium
A nova técnica de soldagem vai possibilitar a fabricação de elementos filtrantes para "Telas Premium", utilizadas especialmente para controle de areia em poços de petróleo e gás. Esse mesmo processo pode ser usado no tratamento de água industrial, filtração em alta pressão e em alta vazão, em saneamento básico, além das indústrias aeronáutica, espacial e em equipamentos científicos.
O Brasil gasta anualmente cerca de US$ 40 milhões em importação de telas desse tipo. Além da economia, o país poderá passar a disputar o mercado internacional do produto, estimado em US$ 200 milhões. Hoje, apenas três empresas no mundo dominam a tecnologia.
A grande participação brasileira nesse mercado se justifica por que a maior parte do nosso petróleo vem de poços de grande profunidade, onde a utilização das telas premium é essencial.
Domínio do ciclo completo
O ciclo completo de produção das telas premium deverá ser dominado pelo Brasil em dois anos, segundo avaliação do engenheiro Samuel Tocalino, da empresa DFB, parceira do LNLS no projeto.
O LNLS trabalha no desenvolvimento de processos especiais de soldagem há mais de 10 anos, para utilização na fabricação de componentes para os aceleradores de elétrons, linhas de luz e outros componentes do Laboratório.
Soldagens não convencionais
"A parceria para o desenvolvimento desse projeto surgiu há dois anos com o interesse comum no desenvolvimento de técnicas de soldagem não convencionais que pudessem unir diferentes materiais metálicos que podem ser utilizados tanto para a fabricação de peças para os aceleradores, como para as outras aplicações," conta o professor Osmar Roberto Bagnato, do LNLS
Assinar:
Postagens (Atom)
About Me
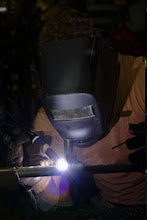
- willianend
- Este blog foi criado com a intenção unica de trocas de informação e experiencias entre soldadores inspetores e todos aqueles que se interessam por esta area de trabalho, peço a todos que ajudem na divulgação e aprimoramento do blog
You can replace this text by going to "Layout" and then "Page Elements" section. Edit " About "
santos
Links
The Flash Radio On Line
!doctype>
Visitantes
Link -me

Deixe seu Recado
BlogBlogs - Últimos Leitores
Tecnologia do Blogger.